Superior MEMS sensors from cavity silicon-on insulator wafer
Superior MEMS sensors from cavity silicon-on-insulator wafers
September 02, 2021 // By Adele Gilliland
Adele Gilliland, applications manager with IceMOS Technology Ltd.
(Belfast, Northern Ireland) looks at how buried
cavities in silicon can be used to enclose MEMS sensors and produce improved
specifications.
Micro electro mechanical systems (MEMS) design provides the basis for several different sensing technologies. According to one recent market forecast, the global MEMS sensors market was valued at US$11.7 billion in 2020 and is expected to reach US$16.8 billion by 2026, providing a compound annual growth rate (CAGR) of 6.5 percent.
Pressure sensors are expected to experience the fastest growth rate due to their utilization in multiple application areas, such as biomedicine, automotive electronics, small home appliances, wearable, and fitness electronics. As pressure sensors become more widely used in the harsh environments found in industrial, automotive and aerospace applications, accurate high temperature pressure measurements will become increasingly important.
MEMS design
Several design and manufacturing approaches are used to integrate monolithically the mechanical structures in the MEMS device to the signal conditioning and other circuitry that add functionality and value to the basic MEMS structure. The two most common approaches are MEMS-first and MEMS-last but there are variations between and within these two extremes.
With a MEMS-first approach, all the processing steps for the MEMS structure, including bulk micromachining, are performed prior to CMOS processing enabling the use of high temperatures that would damage or degrade CMOS. This means that temperatures greater than 1100°C can be used to obtain high-performance silicon on insulator substrates or release the stress in thick deposited polycrystalline silicon layers.
In contrast, a MEMS-last approach, which typically uses surface micromachining to deposit and then etch layers or bulk micromachining for the mechanical structure, must be kept below 400 or 450°C to avoid damaging the existing CMOS circuitry. This means that high performance MEMS materials, such as monocrystalline and polycrystalline silicon, common in inertial sensors and resonators, cannot be used.
The advantages of MEMS-first design, together with the development of stable and CMOS-compatible wafer-level packaging solutions, enable flexible and cost-effective system on chip (SoC) solutions.
Sensors based on silicon-on-insulator (SOI) substrates have an advantage for MEMS devices produced for high-temperature applications because their structures provide greater flexibility in the micro-construction design and greater stability in the application.
Cavity silicon-on-insulator (CSOI) substrates have an even greater advantage over traditional SOI technology because the patterns are bonded facing inward resulting in buried cavities inside the wafer. The result is decreased parasitic capacitance between the device and handle layer of the SOI wafer, allowing for the device to function much more efficiently.
The SOI market is projected to grow from US$1.0 billion in 2020 to US$2.2 billion globally by 2025, at a CAGR of 15.7 percent, according to a Market and Markets report, As a subset of this market CSOI has an equally attractive potential.
The bonding of patterned wafers face-to-face, enables double-side processing of the SOI layer, CSOI also reduces device cost and size without compromising precision. By creating various structures within the cavity, including anchors, beams, pillars and more, developers of MEMS devices have increased design and manufacturing flexibility and it simplifies their silicon processing as well.
Bonding technology for high temperatures
Outsourcing the CSOI allows system designers to develop more intelligent devices by focusing on the value-added circuitry for the most demanding markets. Instead of simply purchasing starting wafers, these engineered silicon substrates enable a company to expand their MEMS sensor offering without making an investment into engineering or equipment resources. Fab managers can use their resources for processing device wafers for finished goods, not making substrates.
Substrate suppliers providing CSOI wafers need deep silicon trench etch expertise coupled with advanced wafer bonding technology to meet customer cavity requirements and create innovative products. Flexibility is also key. In addition to deep reactive ion etching (DRIE), other etching techniques can be used depending on the desired structure and performance. There are various methods of constructing a CSOI wafer and advanced features can be incorporated, potentially opening possibilities that might otherwise not have been considered by the sensor developer.
In its basic form, the IceMOS CSOI technology is two wafers with the cavity etched into one of the wafers and subsequently bonded to the other wafer, creating a vacuum. This process is especially good for sealed absolute pressure sensors because it provides a good quality reference and the cavity is hermetically sealed. As a result, it is the ideal advanced engineering substrate for manufacturing piezoresistive MEMS pressure sensors.
Caption: CSOI is two wafers with the cavity etched into one of the wafers and subsequently bonded to the other wafer, creating a vacuum.
The MEMS pressure sensor works on the principle of the deflection of a thin silicon membrane suspended over the cavity in response to changes in the environmental pressure relative to the fixed pressure within the bonded cavity. The mechanical deformation of the membrane can be converted into an electrical signal using piezoresistive, capacitive or optical detection techniques and the signal conversion and additional circuitry expertise of the sensor manufacturer.
Microphotograph cross-section of a CSOI engineering substrate.
Other more complex structures with multiple bonded silicon layers are available for advanced sensor design. CSOI substrates are the advanced starting wafer for inertial MEMS accelerometers, gyroscopes, and LiDAR sensors, in addition to other MEMS devices such as microphones, speakers, microfluidics, and resonators. With CSOI substrates, developers can make more efficient use of their engineering resources, better manage their MEMS fab capacity loading and cycle times, and, in many cases, reduce new product development and introduction time.
MEMSデザインは異なるセンサー技術の基礎となります。最近のあるマーケット予測によると、世界のMEMSセンサーマーケットの価値は2020年でUS$11.7ビリオン、2026年にはUS$16.8ビリオンに到達し、年成長率は6.5%とされています。圧力センサーは生物医療や自動車エレクトロニクス、小型の家電、着用端末、フィットネスなど、複数の応用分野で使われていることで、最も成長速度が速いと考えられます。圧力センサーはより広く過酷な環境で産業や、自動車、航空宇宙などに使われるにつれ、高温の精度や圧力計測などより重要度が増してきました。
MEMS デザイン
数々のデザインや製造のアプローチで機械的な構造をMEMSデバイスに作り、信号の状態と他の回路が機能することで、MEMSの構造に価値を生み出します。二つの一般的なアプローチとしては、MEMSを先に作るか、後に作るかがありますが、この二つの主流の中で様々なバリエーションの製造方法があります。
MEMSを最初に作成するアプローチでは、すべてのプロセスステップがMEMSの構造のために、バルクの微細加工も含め、CMOSにダメージや劣化を与えてしまうような高い温度をCMOSプロセス作成前に使用することができます。これは1100℃以上の温度を使用して、高いパフォーマンスのSOI基板を製作したり、厚く積層されたポリシリコン膜のストレスを開放したりすることができます。
反対に、MEMSを最後に作成するアプローチでは、一般的に表面の微細加工を施して、各層をエッチングし、バルクを微細加工するので、400℃~450℃以下の温度で、CMOSデバイスへのダメージを避けるように機械構造を作成しなければなりません。これは高いパフォーマンスのMEMS材料、たとえば慣性センサーや共振器などに一般に使用される単結晶や多結晶のシリコンなどは使うことができません。
MEMSを先に製作するデザインの優位性は、安定性とCMOS互換性をともに開発するウエハーレベルのパッケージングソリューションであり、自由度が効き、コスト効果のあるSystem On Chip(SOC)解決法です。
高温用のキャビティーSOI(CSOI)のケースについて
SOI基板を基礎とするセンサーは高温アプリケーション向けのMEMSデバイス製造として優位性があります。なぜならこの構造がより微細な構造の自由度をもち、アプリケーションにおいてより大きな安定性があるからです。
キャビティーSOI(CSOI)基板は伝統的なSOI技術に比べ、より大きな優位性があります。なぜならパターンが張り合わされた表面内部に埋め込み加工できるからです。SOIウエハーのデバイスとハンドル間の寄生キャパシタンスを結果として減らすことができるため、デバイス側の機能を効果的にできます。
SOI市場の一部として、2020年にUS$1ビリオンから2025年までに世界でUS$2.2ビリオンまで増加と見積もられ、2020年から2025年までには15.7%の年平均成長率になる、と市場や市場のレポートは示しており、キャビティーSOIには魅力的な可能性が秘められています。
張り合わされたパターンのウエハーはSOI層の表裏両サイドに加工ができ、CSOIはデバイスコストやサイズを精度を妥協することなく減らすことができます。アンカー、はり、柱など様々な構造をキャビティーの内部に作ることができ、MEMSデバイスの開発者はデザインを多彩に、製造をより自由に、そしてシリコンプロセスをよりシンプルにすることができます。
高温のための張り合わせ技術
キャビティーSOI(CSOI)の外注化によってデザイナーはより高度なデバイスを開発することができ、市場の要求に適した価値のある回路により焦点を当てることができます。ただ単純にスタート材となるウエハーを買う代わりに、こうした技術シリコン基板によって、メーカーにとっては、技術や装置のリソースへの投資をすることなく、MEMSセンサーの発展を簡単に推し進めることができます。工場のマネージャーは装置、時間、お金といったリソースを基盤からではなく、最終製品としてのデバイスウエハーの製造に使うことができます。
CSOIウエハーの基板サプライヤーには、深いシリコントレンチエッチ専門技術と高度なウエハー張り合わせ技術を、お客様のキャビティー要求事項に見合って、かつ革新的な製品を作ることが求められます。自由度も重要な一つです。加えて、深い反応性イオンエッチ(DRIE)やほかのエッチング技術が、求められる構造やパフォーマンスのために使われます。CSOIウエハーや高度な特長を構築するには様々な方法がありますが、潜在的にいろいろな可能性があり、もしかしたら,それらはセンサーの開発者にとっては考えがおよばなかった方法があるかもしれません。
基本的な生産体制として、アイスモスのCSOIは二つのウエハーで、片側のウエハーにキャビティーエッチされたものをもう一つのウエハーに貼り付けして、吸引します。このプロセスが圧力センサーにとっては絶対的にシーリングする重要な要素で、これによりよい品質を生み出し、キャビティーが気密的に封鎖されます。結果、理想的で高度な技術基盤がピエゾ抵抗効果のMEMS圧力センサーを製作します。CSOIはキャビティーエッチされた一つのウエハーともう一方のウエハーの二つのウエハーが張り合わせされ、バキュームして作成されます。
MEMS圧力センサーは、キャビティー上の薄いシリコン薄膜の偏向の原理に作用して、埋め込みキャビティー内の固定圧力に対して、環境の圧力の変化に応じます。機械的な薄膜の変形がピエゾ抵抗効果を使い、容量性、または光学的検出技術と信号変換、そしてセンサー製造者の追加された回路専門技術などによって電気的信号に変換されます。
他のより複雑な構造で複数の張り合わせされたシリコン層を持つような構造も、高度センサーデザインで可能です。CSOI基板は慣性MEMS加速度計、ジャイロスコープ、レーザー画像検出と測距センサー、加えてほかのMEMSデバイスであるマイクロフォン、スピーカー、マイクロ流体力学によって、共振器などの高度なスタートウエハーとなります。CSOI基板により、開発者は技術リソースを効果的に使うことができ、MEMS工場のローディング生産量やサイクルタイムなど、よりよく工程管理することとなり、多くの場合において、新製品の開発や導入時間の削減につながります。
在庫から探す
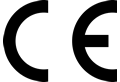
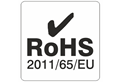